产品制造过程中,任何的不良品产生,皆造成材料、机器、人工等的浪费。任何修补都是额外的成本支出。精益的生产方式,能及早发掘不良品,容易确定不良品的来源,从而减少不良品的产生。【智风绩效】总结,这些浪费包括: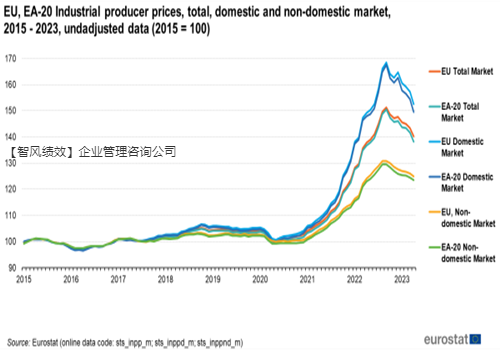
(1)产品报废。
(2)降价处理。
(3)材料损失。
(4)人工设备资源损失。
(5)出货延误取消订单。
(6)信誉下降。
(7)市场份额萎缩。
次品和废品的浪费大家都会比较理解,关键是引起足够的重视,减少不良报废品和返修品的产生。因为这些问题又会带来新的更大的问题,比如因为不良品的产生供应部门要采购更多的材料来预防缺料,这样一来就带来库存的浪费。返修品多了,则需要多配备返修人员,人工的浪费又来了;返修还需要浪费水电气和辅料等成本。因为不良品和返修品太多,有些工厂已经将其纳入正常的预算范围,认为这些不良率是合理的,没有意识到需要改进,这是一个非常危险的问题。任何修补都是额外的成 本支出,因此要尽早发掘次品、废品,寻找、确定次品、废品的来源,从而减少次品、废品的产生。减少次品、废品浪费的关键是第一次就把商品做合格。只有一开始就做好,才能在生产的源头就杜绝次品、废品,杜绝不合格原材料、半成品流入生产后道工序,追求零废品率。
任何的制造现场,都不会将种种浪费自动地展现出来,当然也不会有多少像计算机公司那样,通过工序写实将浪费(如诸多的等待)跃然纸上。且看计算机公司键盘 的加工过程片段:运去检查、等待、运上检验台、检验、登记检查结果、运回装配线、等待,运至底座装配线,其间发生了产品表面划伤不良。如果不能将搬运距离和动作不合理的存在这些根本原因识别出来,划伤之类的问题也很难根本消灭。若要使全部浪费现形出来,必须使其联合制造的产物 异常,现形于表面。发现异常并消除它,只靠少数专家和管理者是远远不能及的,必须依靠全体员工。
所以创建人人都能发现异常的现场是去除浪费的关键。当今众多优秀的制造企业不但在现场运用各种可视化的手段暴露问题,还采用光声、停止动作联合作用的警示灯作为异常问题的"照妖镜"。精益生产方式的思想之一就是要用一切办法来消除、减少一切非增值活动,如检验、搬运和等待等造成的浪费,具体方法就是推行“零返修率”,必须做一个零件合格一个零件,第一次就做好,更重要的是在生产的源头就杜绝不合格零部件、原材料流入生产后道工序,追求零废品率。